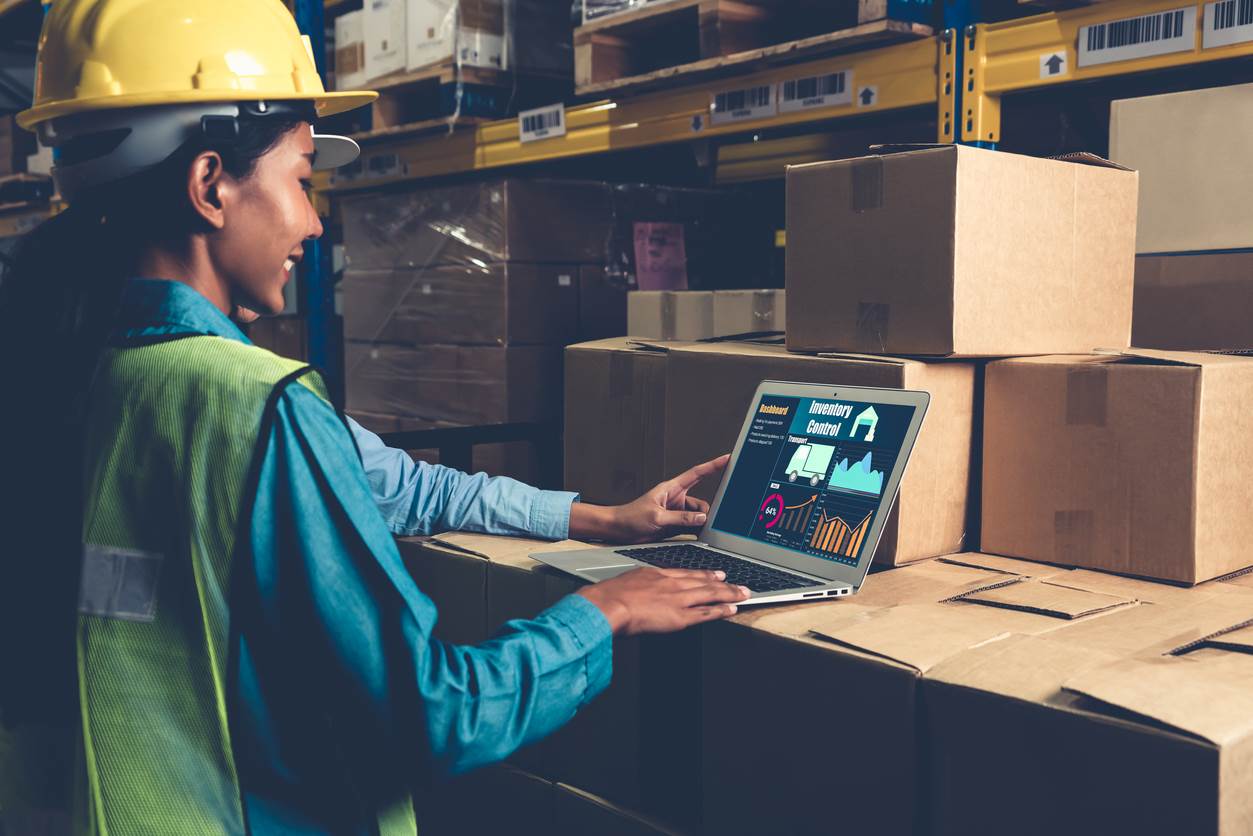
TrulinX Empowers Industrial Engineered Products Distributors Through ERP Business Management Software
With over three decades of expertise, Tribute understands that the project management of engineered products has many variables. We’re here to help by offering an ERP software that can handle many customized options and information management. High-performing distribution companies need a strong ERP business system to manage their day-to-day operations. That’s where TrulinX shows its value. We’ll support you as a strategic partner to help your business run smoother.
ERP Software Designed for Industrial Engineered Products Distributors
For engineered product distributors & fabricators, TrulinX integrates into labor processes to:
- Combat organizational problems
- Enhance collaboration
- Deliver high-quality products on a deadline
TrulinX ERP software has production planning tools designed to meet your needs and challenges. TrulinX's specialized features can help:
- Make scheduling and batch processing more efficient
- Manage, control, and reduce costs
- Offer workflow-based capabilities that enhance the customer experience
- Simplify purchasing and control inventory
- Handle shop floor management and scheduling
TrulinX Software Keeps Production Planning Organized
Distributors and fabricators of design and engineering services need an advanced inventory management system. Whether your facility engineers and distributes:
- Power units
- Control panels
- Power transmissions
- Motors
- Hydraulics
- Pneumatics
- Electrical systems
- Hundreds of other types of industrial equipment
There are several processes that an ERP software solution can help you streamline. These are some of our industry focuses:
- Control circuit relays and accessories
- Push button, selector switches, and pilot industrial controls
- Motor starters, contactors, and controllers
- Industrial electrical relays and switches
- Electric, electronic, and pneumatic controllers for process variables
- Pressure, flow, and process control instruments
- Pressure measurement instruments
- Industrial flow and liquid measuring instruments
- Wire and cable harness assemblies for electronic use
- Industrial and power controls
- Temperature measurement instruments
Labor Burden & Inventory Burden Tracking
TrulinX helps you manage labor, inventory, and time effectively by calculating the burden rate (Labor Burden + Inventory Burden). Labor and inventory burden presents an accurate picture of your gross margins.
The labor burden function allows you to enter labor on a job by the total amount or by tracking time spent by specific employees. The inventory burden allows manufacturers to add indirect material costs to the direct material costs. If a task takes longer than expected to complete, managers need to be able to bill customers accordingly.
In a live example we’ve seen at some industrial shops, it may take an engineer two hours to design an industrial valve. However, a valve's size and complexity can make this process longer. With TrulinX, a distribution manager can manage and track that cost.
Easy Viewing of Pictures & Schematics
Industrial engineered products naturally experience wear and tear over time. When a product becomes damaged or needs parts replaced, it is important to be able to easily refer back to an original schematic, CAD drawing, or an image. TrulinX houses and integrates the documents that outline a product’s design specifications and certifications, which you can easily pull up in the application, email to a customer, or attach to a work order, packing list, etc., such as:
- CAD Drawings
- PDF Documents
- Schematics
- Certificates of Compliance (COFCs)
- Operating Manuals
- Bill of Lading
Work Order Management
TrulinX's work order management function can help:
- Customize every aspect of a customer's order history screens.
- Move the columns around in various ways to find the information you need.
- Reset a query back to its original format.
- Keep track of task-related instructions, cost estimates, the exact scheduling of work, and information about the location and tools required to execute the work order.
Production Management
Engineered product distributors need an efficient and thorough Production Management strategy. Properly managing production capacity requires a careful balance between your available resources and the customer demand or project requirements. Production Management helps distributors:
- Reduce costs
- Prevent stock-outs
- Eliminate excess capacity
- Guarantee the correct number of resources for your supply chain management
- Optimize resource management and allocations
Operation/ Workstation Routing
Accurate work center reporting is crucial for engineered product distributors and fabricators. Real-time data used in the workstation covers:
- Scheduling and formulas used to calculate an operation’s duration
- The formulas that calculate an operation’s costs
- Capacity planning and formulas used to calculate capacity requirements and availability
TrulinX ERP provides a clear-cut way for customers to see the logistics and time necessary to complete an order. With TrulinX ERP, customers will know when a project has moved from painting to welding to testing. Customers will also see the hours allocated to these tasks for billing purposes.
Sophisticated Bill of Materials (BOM’s)
TrulinX software creates an accurate BOM that:
- Avoids production delays
- Decreases operating costs
- Reduces the time it takes to locate missing parts, start another production order, and determine the correct assembly process
- Helps streamline materials requirement planning (MRP)
Shop Floor Management
Managers, sales teams, and shop floor employees can access the same data to keep their operations cohesive. Expand productivity, get a floor-level overview of your facility, and have total control of shop floor operations.
Dispositions Management
TrulinX can help you document when a shop employee pulls an item off the floor, damages a product, or a customer requires a different value or change in the fabrication. TrulinX helps you manage these respective costs whether it is a cost absorbed by the customer or your business.
Actual Vs. Estimated Cost Tracking
TrulinX takes away the experience of using outdated spreadsheets, murky agreements, and manual reporting. It also creates professional purchase orders with pre-defined templates and clear agreements with your suppliers. It saves time and money when manual processes change into an advanced and user-friendly purchase order system.
Industry Partners
One of the ways that Tribute Inc. can best serve each distributor & fabricator’s needs is by knowing their manufacturing partners. We’ve developed a strong rapport with many industry-leading industrial manufacturers in your industry. We work closely with the vendors to help our software users meet vendor requirements and maximize discounts.
Get Started with Tribute Software
TrulinX offers an enterprise resource planning system that helps:
- Automate time-consuming tasks
- Standardize processes
- Focus on your specific business needs with integrated software features
- Provide data reliability and security
- Ensure that you make better business decisions
- Increase your return on investment
Tribute's experts have years of experience with engineered products and working with product distributors and fabricators. We understand the specialized requirements you need and have developed our business management software to meet your niche-focused business needs.
We are more than just a vendor and offer more than just a software package. Our U.S.-based support team provides accommodating software support services to answer all your questions and help keep things running smoothly. We also offer personalized, on-site software implementation and training to help your engineering services set a foundation for success.
Experience the TrulinX difference and fill out a form to request a free demo today! Contact our team for more information on our ERP software for engineered products.