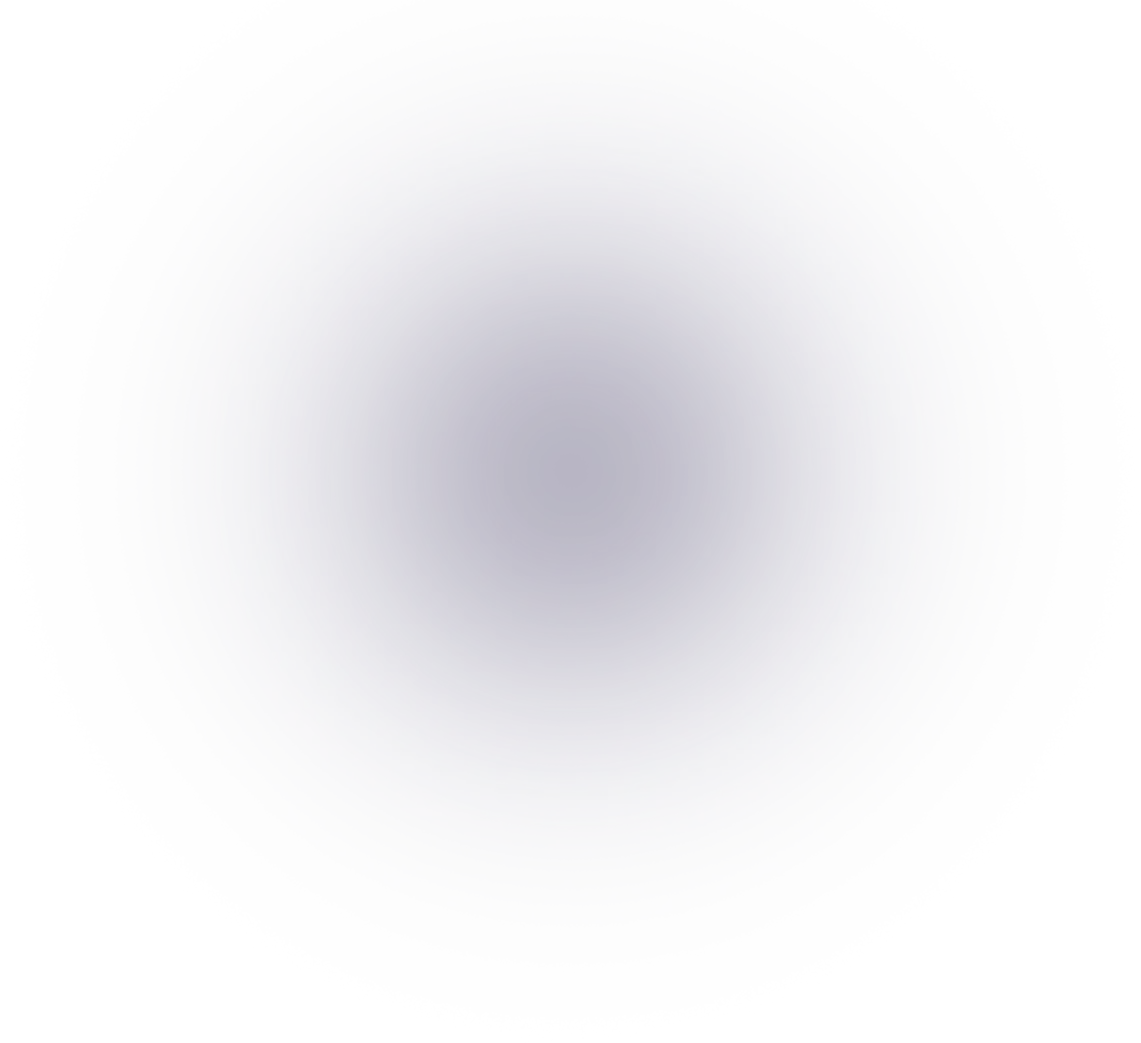
How to Specify & Measure Hydraulic Hose Length to Avoid Hose Failure
Many hydraulic hose installers are not trained on how to correctly specify and measure hydraulic hose length – resulting in potential hydraulic hose failure.
Failed hydraulic hose assemblies have the potential to cause expensive equipment failure and cause catastrophic injuries to your workforce. On top of the risk of potential injury, a hydraulic hose may be too long or short for your application when cut to the wrong length. This slows production and hurts your bottom line. The key to avoiding production slowdown and injury is proper hose assembly.
Proper hose assembly starts with selecting the right hydraulic hose and fittings matched to the application. Let’s take a look at how to correctly specify and measure hydraulic hose length to avoid hose failure and slowdowns.
How to Correctly Measure a Hose Assembly Length
When a hydraulic hose distributor fabricates hundreds of assemblies per day, inches or millimeters matter, and confusion about properly measuring hose length can result in order fulfillment delays, scrap, and extra expense.
When cut to the wrong length, a hose may end up being either a little shorter or a little longer than the specifications call for.
Dennis Sukhanitski, a hydraulic/mechanical engineer, hydraulic specialist, and author of the Fluid Power Pro, has a good article on how to correctly measure a hose assembly length. He states that there are three different ways to measure hose assembly length used in the industry:
- Overall length (OAL) is the total length of the assembly including fittings. This is the default for Parker, Gates, Kuriyama, and several other suppliers.
- Seat-to-seat length is the length of the hose from the bottom of the collar on one end to the internal sealing surface of the other end. This is considered Ryco’s Standard.
- Cut length is the length that the hose and braid are cut to before assembly fabrication. This is the default for EATON.
Keep the following in mind when calculating the OAL:
- Male threaded ends are measured from the end of their threads.
- Female threaded ends and flanged ends are measured from their sealing surface.
- Angled ends are measured from the center of their sealing surface.
- U.S. fittings such as JIC, SAE, NPSM are measured up to the end of the nut.
- DIN, BSP, and ORFS fittings are measured up to the sealing head. This does not include RYCO.
- SAE flange fittings are measured up to the face.
Fabricating a Hose Assembly to the Correct Length Specifications
OAL is the most common way to identify hose length. Unfortunately, there are no standards for the definition of “Overall Length” value, and therefore different manufacturers determine different ways of measuring the value of OAL. In most industrial applications (such as water or general purpose) the OAL is not critical, but in many hydraulic applications, the OAL can be critical due to space restrictions.
The hose cut length for a hose assembly is calculated by subtracting the cut-off factor (distance from the bottom of the ferrule or collar to the end of the fitting or an internal sealing surface).
Hose fabricators need to ensure their staff is assembling the hose to the correct specification to meet the needs of their customers and to avoid creating scrap.
To put the cost of lost inventory in perspective, say you're making 100 hose assemblies with an expensive 4-wire hydraulic hose that costs $10.54 per foot and your fabricator miscalculates the hose length. They now must cut an inch off each end to meet the overall length specifications - that's $174.00 in scrap. On top of that, the amount doesn't include the true replacement cost of the scrap, which can be up to 25 times the original cost (a significantly higher expense at ~ $4,350).
Factors to Consider When Identifying Hydraulic Hose Length
Whether you are identifying hose lengths by OAL, or hose cut length, there are several critical factors to keep in mind to ensure proper hose length, including:
- Machine vibration and motion.
- Routing design.
- Allow enough length so that the fittings are not subjected to pull-off forces when parts reach their limits of travel.
- Avoid stretching the hoses, as this can restrict fluid flow.
- Avoid clamping hoses at their bends to allow for length changes during pressurization.
- Avoid clamping high- and low-pressure lines together.
- Cut the new hose the same length as the one being removed when replacing hoses.
Track Costs and Minimize Error with TrulinX ERP Distribution Management Software
Keeping scrap to a minimum is an essential component to a good ERP software. TrulinX ERP distribution management software streamlines operations for hose fabricators and provides the option of using cut length or overall length when entering a hose assembly BOM, reducing waste and ensuring order accuracy.
As a tenured member of NAHAD with over 38 years in the hose distribution business, Tribute has the industry expertise and capabilities to deliver unmatched ERP solutions for hose and fluid power distributors.
With our niche features, supplier integrations, and industry leadership, TrulinX is specifically designed for your distribution business. Ready to improve your workflow through innovative modern ERP software? Request a Demo to see how we can help you make that change to your business